At VadoTech, our people drive everything we do. In this first edition of our refreshed employee spotlight series, now known as #InsideVadoTech, we catch up with Julian Sieverding, a Project Manager at VadoTech Group. Julian’s career at VadoTech has taken him from being a hands-on test mechanic role to managing projects across continents.
How did your journey at VadoTech begin?
I joined at VadoTech in October 2017 as a test mechanic. My job was primarily working on software updates, system checks, conducting test drives and customer reporting. At the time, I didn’t have any long-term plans but I knew I wanted grow and work internationally.
What drew you to VadoTech?
I’ve always wanted to see more of the world, and VadoTech offered that opportunity. Since joining, I’ve worked in cities such as Beijing and Changchun, with each experience challenging me technically and helping me grow personally.
What is a typical day like for you at VadoTech?
Mornings start early with a cup of coffee. As a project manager, I spend most of my day planning, problem-solving and staying connected with the team. Even though I’m no longer fully hands-on anymore, I stay close to the technical team and offer guidance whenever I can.
What has been your biggest achievement at VadoTech?
Building a high-performing software and debugging team in China. It was rewarding to lead that effort across language and cultural barriers and the team still thrives today.
What’s the best part about working at Vadotech?
The job’s dynamic nature and the people I work with, who keep every day interesting. One day you’re in Changchun, the next in Beijing and then Hefei. That variety keeps things exciting.
What advice would you give someone interested in working at VadoTech?
Be open-minded and willing to step out of your comfort zone. You might come for two years and stay for seven, like me. There’s so much to learn and experience and the opportunity to grow is huge.
Stay tuned for more #InsideVadoTech spotlights as we continue to celebrate the people behind the company.
Are you interested in a career with VadoTech? Explore our current opportunities at vadotech.com/careers.
In celebration of International Women in Engineering Day, we’re excited to highlight Dai Rui, a dedicated team member based in Beijing, China. While her role operates behind the scenes, her precision, teamwork, and commitment play a crucial role in the success of our projects. Her story exemplifies how every contribution, whether technical expertise or operational support, helps shape both the industry and VadoTech.
How did your journey at VadoTech begin?
A friend introduced me to the role. I was searching for a stable opportunity – and yes, the salary was a plus! But beyond that, I found a workplace where people genuinely support one another. Working at VadoTech is one of the best decisions I’ve made.
What does your role consist of?
I oversee billing and financial coordination for our vehicle testing projects. This role requires meticulous attention to detail. I work closely with our engineers to ensure that reports are accurate, invoices are processed correctly, and every financial detail aligns with execution of the project. Every successful project relies on a strong support system, and I take pride in being part of it.
What has been your most memorable experience at VadoTech?
Supporting our winter test drives in Heilongjiang, China. I assisted the team with logistics and provided support to our engineers on-site. It was cold, intense, and filled with challenges, but it also built real teamwork and trust. I learnt a lot from that experience.
What do you enjoy most about working at VadoTech?
The people and the work culture. It’s a comfortable yet professional environment where I feel respected and trusted. When challenges arise, my supervisors are always ready to lend a helping hand. That kind of support motivates me every day.
What does International Women in Engineering Day mean to you?
It signifies inspiration and empowerment.
It serves as a reminder that women belong in engineering – whether in technical positions or supporting roles. The industry thrives on diversity, and I hope more women recognise their value and potential in this field.
Do you have any advice for women entering the engineering field?
Carry out your responsibilities with care and confidence – that alone is a significant contribution. If you can support others, do so, but never underestimate the importance of performing your role well.
About INWED 2025: International Women in Engineering Day (INWED), celebrated annually on June 23rd, is a global initiative organised by the Women in Engineering Society to recognise the contributions of women in engineering and to promote gender diversity in STEM (science, technology, engineering, and mathematics).
Are you interested in pursuing a career with VadoTech? Explore our current opportunities at vadotech.com/careers.
Everyone deserves a second chance - even high voltage batteries! The shift toward electric vehicles (EVs) is putting more batteries on the road than ever before. But what happens when their capacity diminishes? Instead of being discarded, these batteries can serve new purposes, proving that sustainability and innovation go hand in hand.
Why do EV batteries lose capacity?
Modern electric vehicles use lithium-ion cells, which degrade over time. And as storage capacity shrinks, driving ranges get shorter. However, even when an EV battery no longer operates efficiently in a vehicle, it still holds 70-80% of its original energy capacity, making it far from useless.
Repurposing batteries for stationary storage
Instead of discarding batteries, they can be reused in stationary energy storage devices. Stationary use is significantly milder than car use, which subjected batteries to fast charging, discharging, and regenerative braking. They gradually release energy, making them perfect for balancing electrical supply and demand.
HV batteries that have been mustered out from vehicles because their capacity is too low do not become useless or worthless as a result. When these energy storage units are removed from vehicles, they normally have a capacity of around 70-80% of their original energy content. Despite the fact that the capacity of these batteries is no longer enough to use them in vehicles, disposing of them makes neither ecological nor economic sense. These high voltage batteries can continue to be used in a stationary setting in their second life.
For example, in Wendelstein, Germany, decommissioned Audi test vehicle batteries have been reused as a storage facility. Two air-conditioned containers house 84 battery units, which provide one megawatt-hour (1000 kWh) of storage - enough to power 100 houses for a whole day.
How second-life batteries benefit renewable energy
Battery storage is critical to the electricity grid's stability. On bright or windy days, solar and wind farms frequently produce more electricity than is required. Instead of wasting excess electricity, second-life batteries store it and release it when need increases. This contributes to the development of a more reliable and sustainable energy system.
Recycling batteries after their second life
When EV batteries reach the end of their useful life, recycling ensures that important materials are not lost. There are two basic methods for recovering raw materials:
- Thermal processing (melting the batteries down)
- Separates metals based on melting points
- Recovers cobalt, nickel and copper
- Lithium is extracted in an additional step
- Average recycling efficiency: 60-70%, with cobalt and nickel at 95%
- Mechanical shredding (breakdown of components)
- Batteries are shredded in an enclosed container filled with nitrogen to prevent ignition
- Extracts aluminium, copper, graphite, manganese, nickel, cobalt, and lithium
- Has a 96% recycling rate, making it a more sustainable option
The future of battery innovation
High voltage batteries have a purpose even after they have left the road, thanks to second-life applications and innovative recycling processes. As technology advances, new advancements may prolong battery life cycles even further. The future of energy is about more than just producing power; it is also about using it more efficiently.
As electromobility grows, the lifespan of electric vehicle batteries becomes a key focus. For startups like Voltfang, which are driving Europe's mobility and energy transition, ensuring proper battery repurposing is essential. To deepen their expertise, Voltfang's team attended VadoTech's high voltage training in Berlin to gain better expertise in battery handling, safety and second-life applications.
In this blog post, the Voltfang team shares insights into the growing second-life battery sector and explains why specialised training is essential for innovation and sustainability.
Building a sustainable future with second-life batteries
Voltfang envisions a future where eco-friendly energy storage systems work together to build a virtual power station, transforming the way energy is consumed and distributed. The company's mission is clear: to create a more liveable, sustainable world for future generations.
By utilising second-life EV batteries, Voltfang significantly reduces the need for newly mined resources, improving the life cycle assessment of electric vehicles while expanding access to renewable energy storage.
Scaling innovating with Voltfang Industrial Plus
Beyond residential and commercial applications, Voltfang is preparing to launch Voltfang Industrial Plus, a containerised energy storage solution for industrial projects, district-level storage and grid-balancing initiatives. The company leverages high voltage technology to improve energy efficiency, increase storage capacity to megawatt hours and offer a cost-effective solution for large-scale renewable energy storage.
Mastering high voltage safety with VadoTech's training
Proper high voltage training is essential for safely handling and repurposing EV batteries, and Voltfang values workplace safety and technical expertise.
The team attended VadoTech's high voltage training in Berlin, where industry specialists demonstrated battery disassembly, module testing and second-life applications. The state-of-the-art facilities and practical learning approach made VadoTech their ideal choice for further training, equipping Voltfang's engineers with critical safety measures and optimisation techniques for battery repurposing.
Additionally, the on-site training doubled as a team-building exercise, reinforcing Voltfang's commitment to collaboration and innovation in the second-life battery sector.
Driving the future of sustainable energy
As second-life battery solutions evolve, knowledge and skills remain critical for accelerating progress. Voltfang's approach - combining innovative storage solutions with high voltage safety practices - is proving that batteries don't expire; they evolve.
Learn more about the training courses available at VadoTech here.
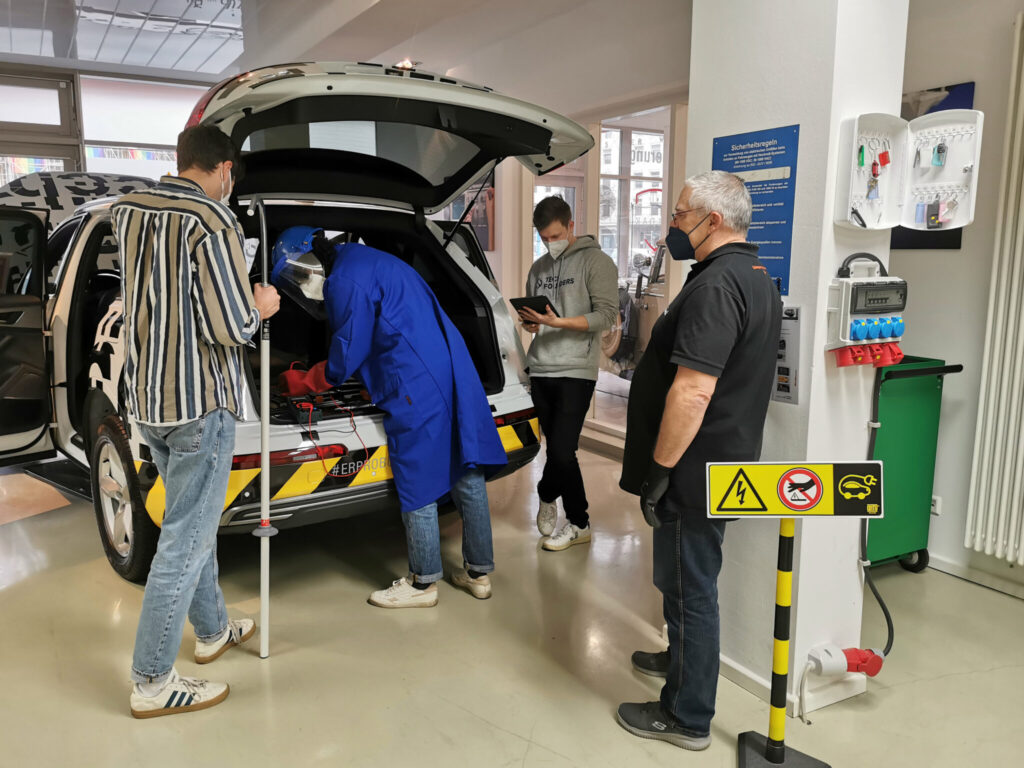
High-voltage on the high seas
High-voltage and the ocean – how do these two things go together? Well, let’s imagine we are taking a boat out to the sea to enjoy nature. Around us is the vastness of the ocean, just the force of nature and relaxation. This romantic image is, however, destroyed with conventional boat drives because of the annoying smell of diesel, loud motor noises and harmful oil pollution. Do alternatives exist?
For a long time there was no environmentally friendly solution. What has become clear in the meanwhile though is that the boat industry must make its contribution to climate protection. The challenge is to reduce the environmental burden and at the same time raise the travelling comfort of taking a boat ride to a new level. Which is exactly where high voltage come into play.
Alternative drives in the boat industry
The boat industry is developing more and more alternative drives. Omega Grey is a young company from Darmstadt which is seizing the opportunity arising from this transformation. The team pursues the goal of making the boat industry more sustainable and digital using an electric drive system with high-voltage technology. As a result unpleasant and disturbing odours, noise and vibrations are a thing of the past. The Omega Grey team describes the advantages of electric mobility in the boat industry and how the VadoTech training centre is helping with regard to the safety of the electric high-voltage systems in this blog post.
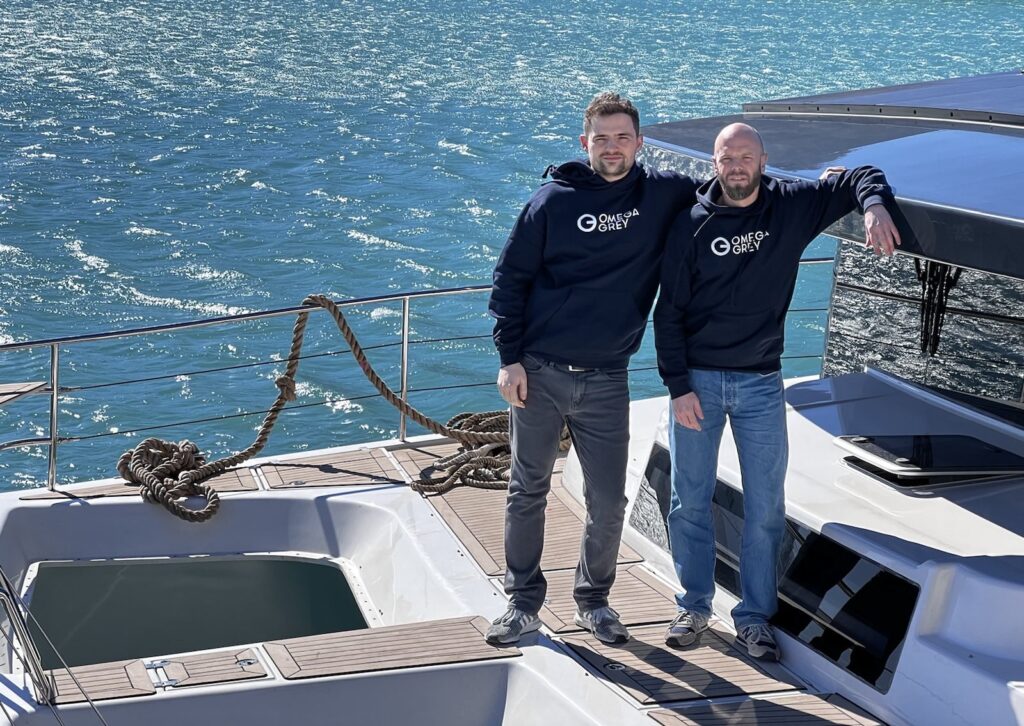
E-boats: sustainable, digital and independent
E-boats have motors that are environmentally friendly and save resources. Omega Grey has therefore developed a reliable drive system for boats as well as yachts. The desire of boat owners for an outstanding travelling experience with smart technology is realised with this system.
To ensure sustainable and intelligent mobility the Omega Grey team does without fossil fuels and relies on electric drives on the water. What is decisive apart from sustainability is the system’s degree of digitisation: The specially developed control unit links the individual components of the drive system such as the battery and motor into an entire system. This can be monitored at any time remotely. The energy flow on the boat can be controlled smartly through this link. Also allowing the remaining reach to be predicted reliably.
Safe drive of an electric boat with a lithium-ion battery
Since conditions on the sea are challenging, the components have to fulfil certain safety standards. With 20 years of experience in the automotive industry, Omega Grey designs the system on the basis of automotive standards. High waterproofness, durability and vibration resistance are critical factors for a reliable drive system. But what does the energy supply look like in practice? The lithium-ion batteries are charged via the shore-side power connection while in port. On the water the solar panels additionally supply the boat with sustainable energy. This even enables an autonomous travelling experience. This independence is also reflected in route planning not being restricted. More and more cities, such as Amsterdam, and protected areas, such as fjords in Norway, are imposing bans on combustion engines. Electric boats are excluded from such bans.
Omega Grey sets sail with 55 feet
After an in-depth test phase of the high-voltage systems and all its components, the drive system from Omega Grey was installed into an all-electric 55-foot catamaran (shown in the preceding section) for the first time in November 2021. Shortly afterwards, in February 2022, the boat was put into operation.
The two installed 100 kW electric motors are driven by eight Mercedes-Benz Energy batteries having a total of 110 kWh. With 10 kWh(p) of solar energy the e-boat can be driven or operated solely with solar energy in optimal conditions. The special feature of the electric catamaran is that it consists of a high-voltage and a low-voltage system. As the following figure shows, the motors are connected with 400 volts to the high-voltage system. The on-board supply, such as the fridge and the air conditioning, are connected with 48 volts to the low-voltage system. The DC/DC converter, in the meantime, ensures the conversion and connection of the two subsystems.
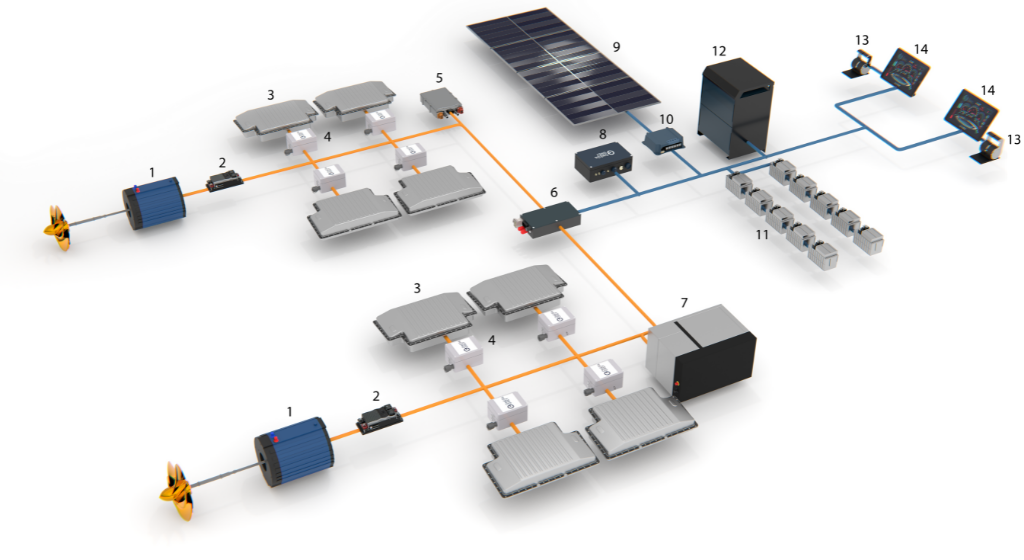
1.High-performance electric motor, 2.Motor controller, 3.HV lithium-ion battery incl. BMS, 4.OG Convert, Module (control unit), 5.Charger (shore-side power), 6.Bi-directional DC/DC converter, 7.Range extender (e.g. diesel generator), 8.OG Connect Module, 9.Solar panels, 10.Solar controller (MPPT), 11.LV lithium-ion battery, 12.DC-AC converter, 13.Drive lever, 14.On-board display
The lithium-ion batteries can be scaled up to an overall capacity of 420 kWh. For additional safety the integrated battery management system (BMS) monitors the batteries around the clock and protects against overheating and excessive discharging. This ensures that the batteries fulfil the highest safety and quality standards such as longevity and waterproofness.
Work safety through high-voltage training at Vadotech
Christian Ophoff, who together with Stefan Strauß, leads Omega Grey, took part in 2020 in VadoTech’s training “AuS - Working under voltage”. The training fully qualifies graduates to work with high voltage. Apart from theory and the legal basics, it was especially the practical exercises which lead to informative experience and an enormous gain in knowledge.
Since the first high-voltage training, the VadoTech Training Centre is the ideal address for Christian to visit further advanced training courses. VadoTech thus also accompanies the growth of Omega Grey by offering further training to become a qualified and recognised responsible electrician. By successfully completing this training, Christian can in the future instruct his employees on how to work with high-voltage systems in electric boats and thus ensure safe work under high voltage at all times.
Christian reports: “The training course has taught me the basics, theoretically as well as practically, to successfully realize my work with Omega Grey. It has helped me in becoming aware once more of the dangers of electricity.” Max Pawolek, VadoTech’s trainer, provided the High-voltage training in a lively manner with discussion sessions and clear and vivid practical examples.
Omega Grey uses the knowledge gained from the high-voltage training for its electric drive systems. These are crucial in particular during safety-critical situations such as the test phase and while commissioning the electric boats. Since special caution is required here, the system is first tested extensively before the high-voltage batteries are connected. After successful measurements and test phases the system is activated and maintained and serviced once a year.
Thanks to VadoTech’s comprehensive training offer, Omega Grey can develop a safe drive system for electric boats and thus pave the way for sustainable mobility on the water.
Stem training: high-voltage training for the formula student team blue flash
The STEM field is certainly no uncharted territory for two female students of the Formula Student Team Blue Flash. Because the future female engineers, in addition to their studies, are working on a race car which first and foremost has to yield high performance while being safe. To keep working as safely as possible under voltage, the two female team members are furthering their knowledge through a high-voltage training course at VadoTech. What the process of the race car manufacturing looks like and how a high-voltage training course helps is described by the two students in a two-part blog post.
From the concept of a race car to its deployment on the race track
Blue Flash Mobility Concepts is a motorsport team from Göttingen founded in 2015.
Each year the team conceives, designs and manufactures its own electric race car prototype and brings it onto the race track.
However, in contrast to usual motorsport teams, Blue Flush does not consist of numerous experienced engineers but rather of 42 students. The race project is realised by the students during their free time besides their studies. Jonas Antonczyk, team leader during the season 2021/22 said: “Our team members on average work approx. 20 hours per week on this project besides their lectures and thus manage to build a high-performance racing car within only eight months.”
Blue flash enters the race electrically and sustainably
With the self-made electric race car Blue Flash takes part in international competitions every year. The team competes against more than 200 other teams in their class in races against time.
These competitions are run under the umbrella project “Formula Student” where future engineers gain experience in a professional context at an early stage. The Formula Student is an international design competition, divided into the three classes “Combustion”, “Electric” and “Driverless”. Blue Flash has been participating in the Electric class since its team formation. The team has been using high-voltage drives since 2018 with the aim of efficiently exploiting the full 80 kW of power specified by the Formula Student regulations. The 450 V battery required to this purpose is designed and manufactured by the students themselves. Only the Lithium-Polymer cells (LIPO) are bought.
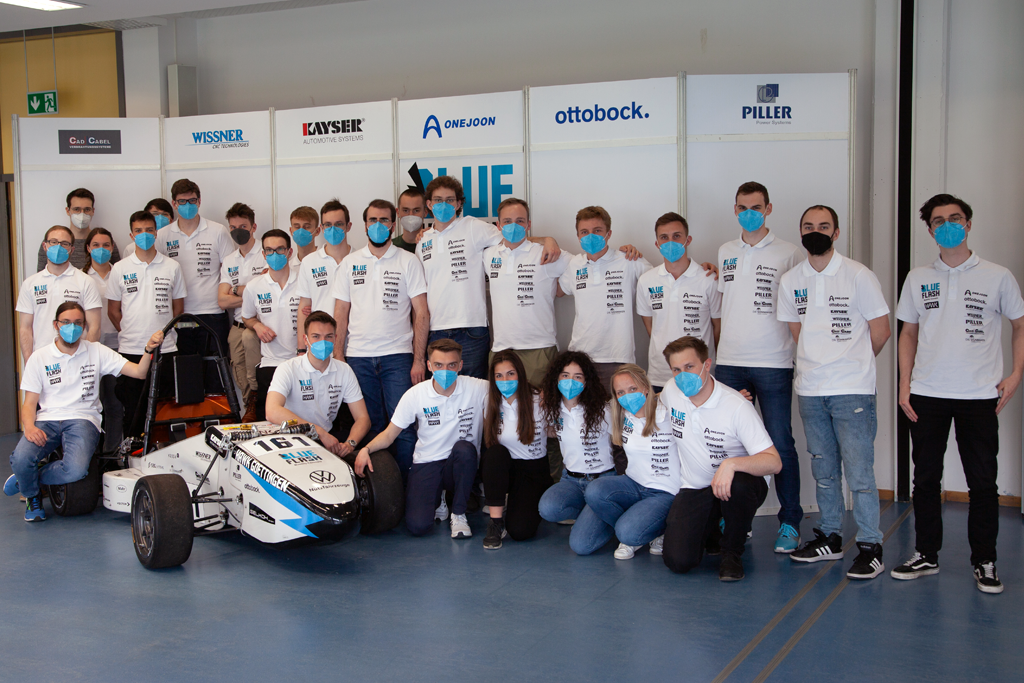
Previous achievements in the formula student
In addition to the performance of the vehicle, the presentation by the students is rated as well. Around one third of the overall ranking consists of the “static disciplines”. The team members present their developments, the costs as well as a fictitiously developed marketing campaign for their car to a jury from the automotive industry.
With a place in the top 15, Blue Flash excelled in both their competitions last season. The students got particularly good results in the Cost Report with a second and fourth place.
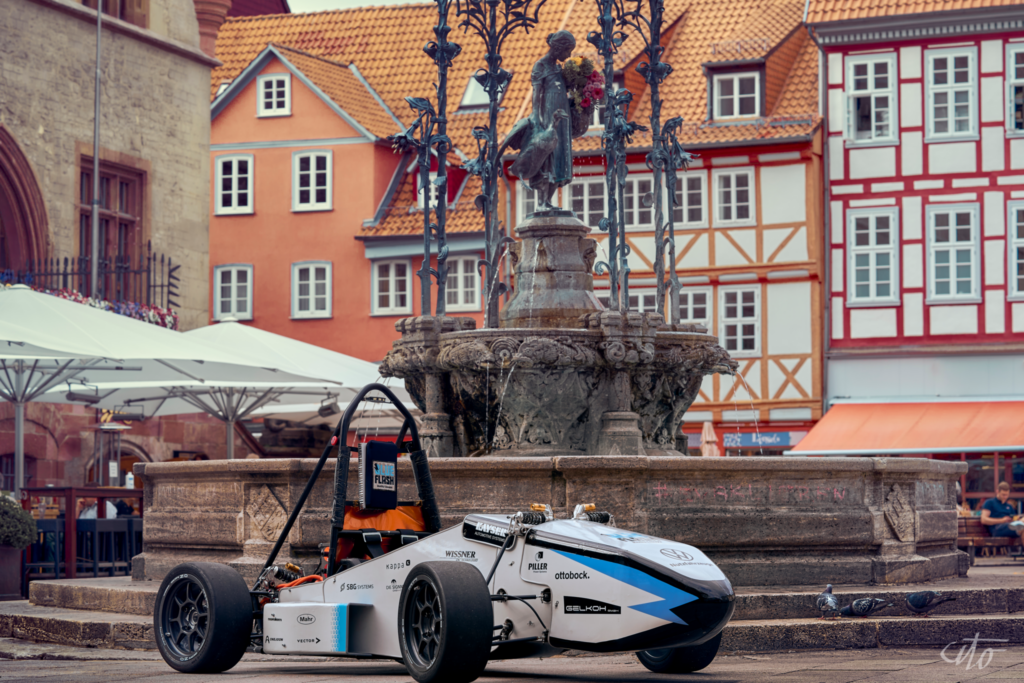
Cooperation between Vadotech and Blue Flash
Apart from the performance, the subject of safety has been one of the main focuses of the team from the very start. In 2017 the team won a Special Award for the fire extinguisher it had integrated in the battery box – which made it the safest car in the entire competition.
To maintain safety at the highest level even during the development process, the team in 2017 members searched for a partner to support the students in their undertaking. At the beginning of 2018 Blue Flash found the ideal partner in VadoTech’s training centre for the plan of further training in the area of high-voltage safety.
Safe work in a high-voltage environment through further training at Vadotech
Through targeted further training for the team members to become “Electrical System Officers” (ESOs) the team ensures the best possible safety during the entire development and testing process. The further training is divided into two main fields.
With further training as a skilled person (FHV) of the levels 2E and subsequently 3E according to the guideline DGUV I 209-093 at VadoTech the students achieve a general in-depth understanding of dealing with high-voltage systems and of working with live-components.
In addition, the qualified electrician (vEFK) at the university (HAWK) is already being prepared in corresponding further training to support and train the ESOs in their work.
In a second step the prospective Electrical System Officers are then trained by experienced ESOs in dealing with team-specific working methods and regulations. These then autonomously implement the development of the high-voltage components.
Further training in the stem field – experience report by the female students
In April 2022 two of Blue Flash’s prospective ESOs, Lea and Lisa, completed the further training to become FHVs and receive the authorisation to work under voltage. Lea said: “Through the training at VadoTech I now have a deeper understanding of the dangers of electric current.” “As a result I now feel secure in working on high-voltage systems which I would not have dared to do beforehand.” Lisa added: “Uwe Rahm, VadoTech’s trainer, underpinned the theoretical parts with good practical examples and spent a lot of time answering individual questions”. In particular working on the Audi Q7 e-tron, which is available in VadoTech’s cutting edge equipped training rooms, helped both of them learn to work safely in a high-voltage environment. Further training participants were also from the STEM field which resulted in an exchange of experience with interesting discussions.
Cooperation with Vadotech is extended
Moritz Borchert, team leader for the season 2020/21, said: “Through the cooperation with VadoTech we have so far always been able to present one of the safest cars at the races.” The team is continuing its cooperation with the training centre. Currently further team members are again participating in a high-voltage training course on-site in Berlin. The second part of the blog post then includes a report on the development process of the race car and what influence the knowledge resulting from the training has on it.
After two and a half years of global disruptions caused by the COVID-19 virus, the long-awaited moment has arrived - VadoTech employees can once again travel to China. In September, four new team members prepared for their international assignments by participating in a high voltage training course at our Berlin training center. We had the opportunity to speak with three of them - Alexander Lunkes, Marcos Gomez, and Manuel Weidenfeller about their unique application experiences and expectations for the journey ahead.
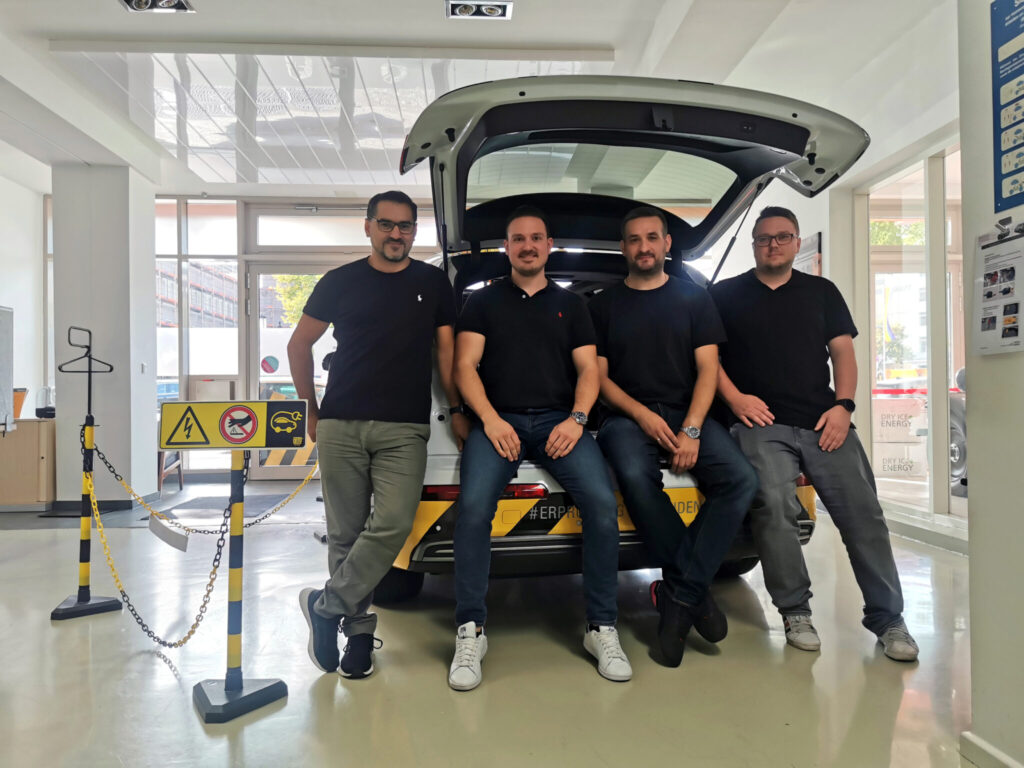
Meet our new team members
Alexander (30) comes from the Bitburg area and is a trained automotive technician. His career has already taken him to Luxembourg, Belgium, the Netherlands, Switzerland, Austria, and France, where he worked in various roles, including vehicle construction, materials handling, and service management in the commercial vehicle sector. In his free time, Alexander enjoys long road trips and cross-country travel.
Manuel (31) hails from Montabaur and recently earned his master craftsman certification in Koblenz - finishing at the top of his class. Prior to that, he worked as an automotive mechatronics technician and underwent further training to become an automotive service technician. Manuel enjoys spontaneous weekend getaways and exploring new destinations.
Marcos (46) has a background in the automotive industry, starting his career as an automotive electrician before advancing to service technician and chief mechanic. He later took on the role of workshop manager. Outside of work, Marcos restores classic vehicles, rides motorbikes, and participates in mud races.
Insights from our new team
VadoTech: Our recruitment team is thrilled to have you on board. You’re among the first employees to be assigned to China since the pandemic began. Marcos, your hiring process started quite a while ago. Do you remember when your interview took place?
Marcos: My interview at VadoTech was back in 2019, and I have very positive memories of it. I spoke with a recruiter and an electrical engineer who had previously travelled internationally with VadoTech. I received a lot of direct insight during the discussion, which immediately sparked my interest. The pandemic pause allowed me extra time to consider my decision, and ultimately, I became even more certain about taking on this opportunity.
VadoTech: We’re fortunate that you remained patient! Despite the long wait, how did you find the application process?
Marcos: The entire process was smooth. There were moments during the pandemic when I lost hope that things would work out, but VadoTech kept me well-informed throughout. I never felt forgotten.
VadoTech: That’s great to hear! How did you first come across our job listing?
Alexander: I found it through a simple Google search, which led me to your website and YouTube videos. Manuel: I was searching for jobs in Asia and ended up on your site. The engaging videos and welcoming recruiter really made a strong impression on me. Marcos: I wasn’t looking specifically for this job, but I searched for “chief mechanic” on Indeed. I wanted to move away from traditional dealership work and explore new career paths.
Why Vadotech?
VadoTech: What convinced you to join us?
Manuel: The adventure! And the recruiter really made a difference. Alexander: I saw a great opportunity for personal and professional growth at VadoTech. Many of the locations where VadoTech and Zynit operate are highly appealing to me. Additionally, being part of AB Dynamics offers even greater career development opportunities. Marcos: The recruitment process helped answer many of my questions. I was eager to try something new and shift to a different side of the automotive industry. The combination of cutting-edge technology and an international assignment sealed the deal for me.
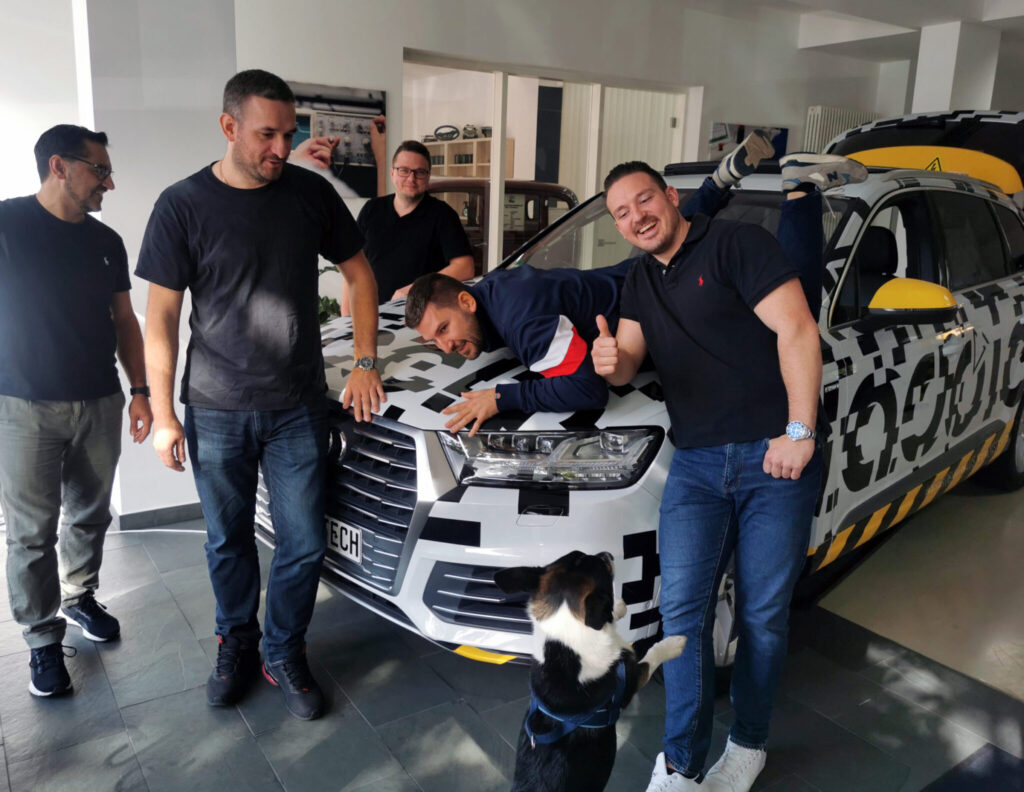
Expectations for China
VadoTech: Manuel, you recently passed your master craftsman’s exam in Rheinland-Pfalz as the top student in your class - congratulations! What are your goals in China?
Manuel: Honestly, I’m taking the plunge with an open mind. I know that working with the latest automotive technologies will create exciting opportunities for the future.
VadoTech: Alexander, you have a passion for travel. Have you ever been to China?
Alexander: Not yet! I’ve visited Indochina, but this will be my first time in China.
VadoTech: What attracted you to this assignment?
Alexander: I wanted to experience a country that’s difficult to visit as a tourist - somewhere vastly different from Germany.
VadoTech: Do you already have an idea of what to expect culturally, or are you approaching it with an open mind?
Manuel: I’m eager to immerse myself in a new and adventurous culture. Marcos: Visiting the Great Wall of China is definitely on my bucket list - I need to see it with my own eyes.
VadoTech: Are you concerned about quarantine measures related to COVID-19?
Manuel: Ten days in a hotel? Sounds like an opportunity to relax! [laughs] Marcos: I plan to use the time wisely - I’ll prepare for my Chinese driving licence. With books, podcasts, and Duolingo, the days will go by quickly.
Preparing for the job
VadoTech: Here in Berlin, you're undergoing high voltage training before heading to China. What are you learning?
Marcos: Safety protocols and procedural knowledge for working with high voltage systems - it’s essential training. My previous experience in this field was basic, so this course has been incredibly valuable. Alexander: We’re also gaining important insights into vehicle development, which will be useful in China.
VadoTech: Before we wrap up, what advice would you give to future applicants considering a role at VadoTech?
Manuel: Just go for it! Marcos: Keep an open mind and listen - you’ll learn a lot.
Thank you for taking the time to speak with us! We’re excited to welcome you to our team and wish you a successful assignment in China.
Would you like to join VadoTech? Click here to explore job opportunities.
We’re delighted to share an exciting new chapter in our journey: VadoTech Zynit is now proudly part of the AB Dynamics Group.
Founded in 1982, AB Dynamics is a leading global provider of automotive test and verification solutions. Their extensive portfolio includes the development and testing of advanced driver assistance systems (ADAS), high-performance driving simulators for motorsport and research, as well s comprehensive validation services for both individual components and complete vehicles.
This next chapter strengthens our capabilities and broadens our reach in international vehicle testing, while ensuring continuity in the service and expertise our global customers rely upon. The way we collaborate with you will remain unchanged - you are assured of the same dedicated teams and industry-leading quality as always.
As we progress, we are already testing the technologies of tomorrow and are eager to shape the future of mobility together. New collaborations, challenges, and greater opportunities are on the horizon.
To learn more about AB Dynamics and their pioneering work in testing and development, please visit: www.abdplc.com
It will take two and a half weeks until we see the serial version of the Taycan from Porsche. Until then, the near-series Taycan will undergo an endurance test on the high-speed track in Nardò (Italy). There the Taycan covered exactly 3,425 kilometres within 24 hours. This corresponds approximately to the distance from Nardò to Trondheim (Norway). On average, the electric sports car travelled at speeds of 195 to 215 km/h over the distance.
The Taycan thus definitely proves its long-distance quality at outside temperatures of 42 degrees Celsius at the peak and an asphalt temperature of up to 54 degrees Celsius. The pre-series Taycan only had to stop for quick loading stops and driver changes. Six Porsche test drivers were at the start to complete the quality assurance test in 24 hours as part of a hot country endurance test.
The Taycan did this exhausting long distance run without any problems. The result in Nardò underlines the advantages of the unique 800 Volt technology and its high degree of maturity. Before the Taycan is launched on the market at the end of the year, we will have completed more than six million test kilometres worldwide.
Stefan Weckbach, Series Manager Porsche Taycan
The Taycan will be the first series-produced electric vehicle to hit the road with a system voltage of 800 volts. The 800-volt technology enables high continuous output, reduces charging time and reduces the weight and installation space of the wiring. 800 Volt High Power Charging columns from Porsche Engineering Group GmbH were used for the endurance run in the Nardò Technical Center. In addition, the sophisticated thermal management of the Taycan contributed to the fact that an average of 143 km per hour could be covered consistently.
At the heart of Taycan thermal management is a highly efficient, intelligent system for cooling and heating high-voltage components. This prevents possible power losses due to excessive heat development and ensures that the optimum temperature for the most efficient charging process is available when the charging station is reached.
Source: Porsche AG – Press Release dated August 19, 2019
Everybody knows them and everybody knows what they're for. But at least they know what they are capable of. We are talking about wind turbines. Guess what: How many revolutions does a wind turbine with 7.5 megawatts (MW) need to completely charge an electric vehicle with 100 kilowatt hours (kWh) battery capacity?
There are only ten revolutions which do not last longer than one minute. Even smaller wind turbines with only 3.3 MW require only 24 revolutions. For example, a modern wind turbine can supply around 4000 electric cars with electricity in one year if it is assumed that an average electric car needs around 2500 kWh per year. If the vehicle has a low battery capacity, such as Teslas Model 3, the battery (50 kWh) can be fully charged with only 5 revolutions.
But how environmentally friendly is this solution, electric cars in combination with a wind turbine? A large electric vehicle such as the Tesla Model S or Model 3, for example, can only make up for its carbon footprint from production after about eight years. A Golf, on the other hand, can claim this after only three years. Wind turbines can take off their CO2 backpacks much faster. After around 4 to 7 months, a wind turbine is climate-neutral.
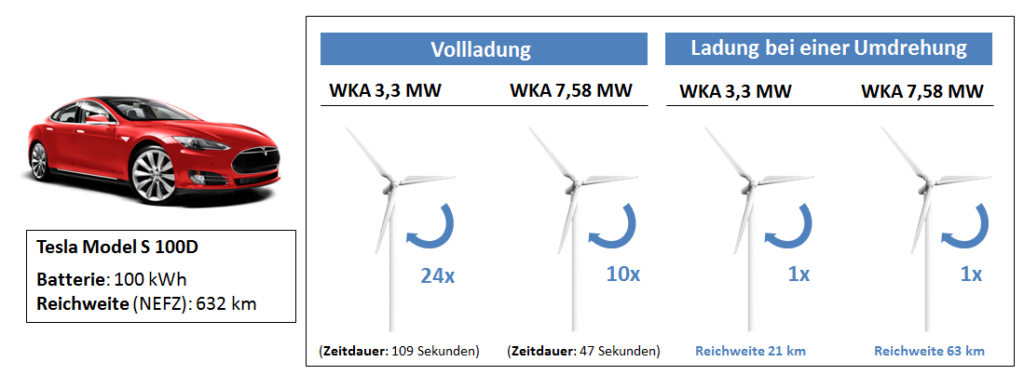