MINT-WEITERBILDUNG: HOCHVOLTSCHULUNG FÜR DAS FORMULA STUDENT TEAM BLUE FLASH
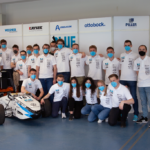
Der MINT-Bereich ist für zwei Studentinnen des Formula Student Teams Blue Flash kein Neuland. Die angehenden Ingenieurinnen arbeiten nämlich neben ihrem Studium an einem Rennwagen, der vor allem performant und sicher sein muss. Um auch zukünftig unter Spannung so sicher wie möglich zu arbeiten, bilden sich die beiden Teammitgliederinnen bei einer Hochvoltschulung von VadoTech weiter. Wie der Prozess der Rennwagenfertigung aussieht und wie eine Schulung zum Thema Hochvolt dabei weiterhilft, beschreiben die Studenten in einem zweiteiligen Blog-Beitrag.
Blue Flash Mobility Concepts ist ein in 2015 gegründetes Motorsportteam aus Göttingen.
Jedes Jahr konzeptioniert, konstruiert und fertigt das Team einen eigenen elektrischen Rennwagen Prototypen und bringt diesen auf die Rennstrecke.
Allerdings besteht Blue Flash nicht wie die üblichen Motorsportteams aus einer Vielzahl von erfahrenen Ingenieuren, sondern aus 42 Studierenden. Das Rennprojekt setzen die Studierenden während ihrer Freizeit neben dem Studium um. „Unsere Teammitglieder arbeiten im Schnitt ca. 20 Wochenstunden neben ihren Vorlesungen an diesem Projekt und schaffen es dadurch innerhalb von nur acht Monaten einen performanten Rennwagen zu bauen.“, erklärt Jonas Antonczyk, Teamleiter in der Saison 2021/22.
Mit dem eigengefertigten Elektro-Rennwagen nimmt Blue Flash jährlich an internationalen Wettkämpfen teil, bei denen sich das Team in Rennen gegen die Zeit mit über 200 weiteren Teams in ihrer Klasse misst.
Diese Wettkämpfe laufen unter dem Dach-Projekt „Formula Student“, bei dem die angehenden Ingenieur*innen frühzeitig Erfahrung im professionellen Kontext sammeln. Die Formula Student ist ein internationaler Konstruktionswettbewerb, welcher sich in die drei Klassen „Combustion“, „Electric“ und „Driverless“ aufteilt. Blue Flash nimmt bereits seit der Teamgründung in der Electric-Klasse teil. Um die vollen 80 kW Leistung, die das Reglement der Formula Student vorgibt, effizient auszuschöpfen, fährt das Team seit 2018 mit Antrieben im Hochvolt-Bereich. Die dafür benötigte 450V Batterie entwerfen und fertigen die Studierenden selbst. Nur die Lithium-Polymer Zellen (LiPO) kaufen die Mitglieder ein.
Neben der Performance des Fahrzeugs wird auch die Präsentation der Ingenieurinnen bewertet. Rund ein Drittel der Gesamtwertung kommt aus den „statischen Disziplinen“. Die Teammitgliederinnen stellen vor einer Jury aus der Automobilbranche ihre Entwicklungen, die Kosten sowie eine fiktiv entwickelte Vermarktung ihres Fahrzeugs vor.
Mit einer Platzierung in den Top 15 glänzte Blue Flash auf ihren beiden Wettkämpfen in der vergangenen Saison. Besonders gute Ergebnisse erzielten die Student*innen mit einem zweiten und vierten Platz im Cost Report.
Von Anfang an ist neben der Performance das Thema Sicherheit ein Hauptaugenmerk des Teams. 2017 gewann das Team einen Special Award für ihren in den Akku-Kasten integrierten Feuerlöscher, welcher das Auto zu dem sichersten Fahrzeug des gesamten Wettkampfes machte.
Um die Sicherheit auch während des Entwicklungsprozesses auf dem höchsten Niveau zu halten, begaben sich die Teammitglieder*innen noch 2017 auf die Suche nach einem Partner, der die Studierenden bei diesem Vorhaben unterstützt. Anfang 2018 hat Blue Flash mit dem Schulungszentrum von VadoTech den idealen Partner für die angestrebten Weiterbildungen im Bereich Hochvoltsicherheit gefunden.
Durch gezielte Weiterbildungen der Teammitglieder*innen zu sogenannten „Electrical System Officers“ (ESOs) gewährleistet das Team während des gesamten Entwicklungs- und Testing-Prozesses bestmögliche Sicherheit. Die Weiterbildung teilt sich dabei im Wesentlichen in zwei Bereiche auf.
Mit der Weiterbildung zur fachkundigen Person (FHV) der Stufen 2E und anschließend 3E nach DGUV I 209-093 bei VadoTech erreichen die Studierenden ein tiefgreifendes Verständnis im allgemeinen Umgang mit Hochvoltsystemen und beim Arbeiten an unter Spannung stehenden Komponenten.
Zusätzlich wurde die verantwortliche Elektrofachkraft (vEFK) an der Hochschule (HAWK) in einer entsprechenden Weiterbildung bereits darauf vorbereitet, die ESOs in ihrer Arbeit zu unterstützen und zu schulen.
Im zweiten Schritt werden die angehenden Electrical System Officers dann durch erfahrene ESOs im Umgang mit den teamspezifischen Arbeitsweisen und Vorschriften geschult. Diese setzen anschließend die Entwicklung der Hochvoltkomponenten eigenständig um.
Im April 2022 absolvierten zwei angehende ESOs von Blue Flash, Lea und Lisa, die Weiterbildung zur FHV und die Berechtigung zum Arbeiten unter Spannung in Berlin. „Durch die Schulung bei VadoTech habe ich jetzt ein tiefer gehendes Verständnis zu den Gefahren des elektrischen Stroms“, berichtet Lea. „Dadurch fühle ich mich nun sicher, an Hochvolt-Systemen zu arbeiten, was ich mich vorher nicht getraut habe.“ Lisa ergänzt: „Uwe Ramm, der Trainer von VadoTech, hat mit guten Praxisbeispielen die Theorieanteile untermauert und sich viel Zeit für individuelle Fragen genommen.“ Besonders das Arbeiten an dem Audi Q7 e-tron, der sich in den modern ausgestatten Schulungsräumen von VadoTech befindet, hat beiden dabei geholfen, das sichere Arbeiten im Hochvoltumfeld zu erlernen. Die weiteren Schulungsteilnehmer kamen ebenfalls aus dem MINT-Bereich, sodass sich ein Erfahrungsaustausch mit spannenden Diskussionen ergab.
„Durch die Kooperation mit VadoTech haben wir es bisher immer geschafft, eines der sichersten Fahrzeuge auf den Wettkämpfen zu präsentieren“, erzählt Moritz Borchert, Teamleiter der Saison 2020/21. Die Zusammenarbeit führt das Team mit dem Schulungszentrum weiter fort. Aktuell sind bereits weitere Teammitglieder wieder bei einer Hochvoltschulung in Berlin vor Ort. Im zweiten Teil des Blog-Beitrags folgt dann ein Bericht über den Entstehungsprozess des Rennwagens und welchen Einfluss das erlernte Schulungswissen darauf hat.
Sie müssen den Inhalt von reCAPTCHA laden, um das Formular abzuschicken. Bitte beachten Sie, dass dabei Daten mit Drittanbietern ausgetauscht werden.
Mehr Informationen